Wind energy conversion involves multiple engineering domains including fluid dynamics, solid mechanics, electromechanics, and control. The dynamics of this process are further coupled with the response of the structural components of this system. External factors, such as the wind and wave conditions and the amount of energy demand also determine the system response. My work has focused on methods to capture the interactive effects of multiple physical systems, the operating context, and changes that occur over time [4, 6, 7]. Component reliability promotes sustainability and is a starting point for the work. To understand reliability, it is necessary to explore the interactive effect over time. I have demonstrated an application of this work is in the integrated design and control framework for a variable ratio gearbox for wind turbine applications. This framework provides a combination of gearsets that promote maximum total lifetime energy production, reliable component life, and minimal material use. In more recent work, my research group, the ESDRG, has developed a comprehensive framework for the aerodynamics design (the modeling procedure is discussed in the next section), structural design, mechanical assembly, and control, of an adaptive wind turbine blade. The framework facilitates the commercialization of this work [1, 8-10]. It does this through the incorporation of the manufacturing process and commercially available components in the framework.
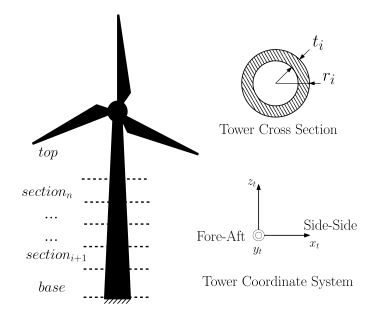
Wind turbine tower parameters
Additions to this framework include the consideration of blade stress [2], optimal components life (versus maximum components life) [5], tower life and environmental impact [11], environmental impact of materials, and upgradeable component design. An outcome of these studies has been the of a gearbox design. The work indicates the gearbox can improve energy production by up to 10%. Additionally, the ESDRG has developed an adaptive blade for wind energy systems. Simulation work modeling suggests a gain in the range of 4 to 12% may be achieved at the rated speed, while a load reduction of up to 70% may be possible during full-load operation. The generality of these frameworks means each can be used for other applications, such as automotive mechanical gearboxes, aircraft, and rotorcraft.
1. Khakpour Nejadkhaki, H. and J.F. Hall, Control Framework and Integrative Design Method for an Adaptive Wind Turbine Blade. Journal of Dynamic Systems, Measurement, and Control, 2020. 142(10).
2. Nejadkhaki, H.K., A. Lall, and J.F. Hall, A Methodology to Synthesize Gearbox and Control Design for Increased Power Production and Blade Root Stress Mitigation in a Small Wind Turbine. Journal of Mechanical Design, 2017. 139(8): p. 081404.
4. Hall, J.F., Palejiya, Dushyant, Shaltout, Mohamed L., Chen, Dongmei, An Integrated Control and Design Framework for Optimizing Energy Capture and Component Life for a Wind Turbine Variable Ratio Gearbox. Journal of Solar Energy Engineering-Transactions of the Asme, 2015. 137(2): p. 021022.
5. Pasquali, F., et al., Method for design life of energy system components based on Levelized Cost of Energy. Journal of Cleaner Production, 2020: p. 121971.
6. Hall, J.F., Chen, Dongmei, Dynamic Optimization of Drivetrain Gear Ratio to Maximize Wind Turbine Power Generation-Part 1: System Model and Control Framework. Journal of Dynamic Systems Measurement and Control-Transactions of the Asme, 2013. 135(1): p. 011016.
7. Hall, J.F., Chen, Dongmei, Dynamic Optimization of Drivetrain Gear Ratio to Maximize Wind Turbine Power Generation-Part 2: Control Design. Journal of Dynamic Systems Measurement and Control-Transactions of the Asme, 2013. 135(1): p. 011017.
8. Nejadkhaki, H.K., et al., A variable twist blade for horizontal axis wind turbines: Modeling and analysis. Energy Conversion and Management, 2021. 248: p. 114771.
9. Mou, F., et al., Weighted Least Squares Approach for an Adaptive Aerodynamic Engineered Structure With Twist Transformation. Journal of Energy Resources Technology, 2019. 141(5): p. 051207-051207-11.
10. Hamid Khakpour Nejadkhaki, J.F.H., Modeling and Design Method for an Adaptive Wind Turbine Blade With Out-of-Plane Twist. Journal of Solar Energy Engineering, 2018. 140(5): p. 9.
11. Pasquali, F.M. and J.F. Hall, Computing Marginal Cost of Durability of Energy Systems Components by Structural Optimization With Fatigue Constraints. Journal of Energy Resources Technology, 2021. 144(6).