The performance of a complex system depends on the system design, how it operates, and the materials and manufacturing methods that are available to build this system [1]. Consider system life, which is highly dependent on all these domains. A durable design can tolerate a higher degree of wear and tear, and thus, provides more flexibility to operate the system across a broader range of conditions [2]. Conversely, the operational demands must be lighter for a physical design that lacks durability and or stability. Since this physical design is bound by materials properties and available manufacturing processes, the control design is connected to these attributes as well.
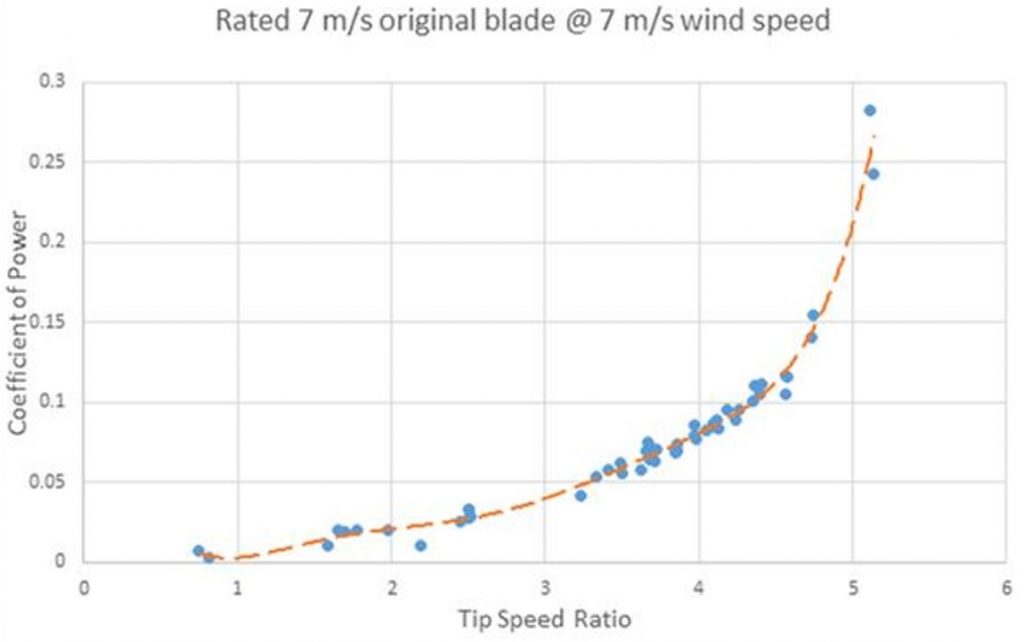
Sample data from Region 2 study (conducted in UB wind tunnel) of wind turbine models
There are also inputs and outputs to the system that transcend the physical design. Once the system is deployed it is uncertain exactly how these environmental factors will be applied over time. Examples of these factors include the nature of the wind that a wind turbine experiences, the energy demanded of these systems, the road upon which a vehicle is driven, and the nature in which a human operates the vehicle. These factors can also be difficult to identify, understand, and quantify [3]. Nevertheless, these challenges can be overcome. Consider the method used to predict gear-tooth pitting [4]. It combines parameters indicative of the physical design with those that describe the external loading. The mathematical framework further lends itself to critical qualitative information, such as that which describes the customer’s need for reliability. In recent work, I have shown how a framework can be devised to incorporate qualitative needs for energy demand.
There exists a set of mathematical relationships that describe the interaction among the multiphysical and multidisciplinary parameters in the complex system. In addition, these relationships change over time. There are also issues related to how degenerative events, such as mechanical and thermal wear affect the capability of the controller over time. These relationships could facilitate concurrent engineering design. The simultaneous understanding of all the critical events makes it possible to explore the design space, look at trade-offs among design and performance objectives, and achieve robust design and operation [5]. Nevertheless, the relationships are not readily understood due to the number of parameters, the complexity of the system, and the onerous task of simulating performance through computational resources. Thus, there is a need for methods and tools that explore these relationships in the context of system design.
1. Khakpour Nejadkhaki, H. and J.F. Hall, Control Framework and Integrative Design Method for an Adaptive Wind Turbine Blade. Journal of Dynamic Systems, Measurement, and Control, 2020. 142(10).
2. Nejadkhaki, H.K., A. Lall, and J.F. Hall, A Methodology to Synthesize Gearbox and Control Design for Increased Power Production and Blade Root Stress Mitigation in a Small Wind Turbine. Journal of Mechanical Design, 2017. 139(8): p. 081404.
3. Suk, H., et al., Socio-Technical Modeling to Manage Power Distribution for Microgrid Systems With Limited Production Capacity. Journal of Solar Energy Engineering, 2021. 144(1): p. 011010.
4. Hall, J.F., Palejiya, Dushyant, Shaltout, Mohamed L., Chen, Dongmei, An Integrated Control and Design Framework for Optimizing Energy Capture and Component Life for a Wind Turbine Variable Ratio Gearbox. Journal of Solar Energy Engineering-Transactions of the Asme, 2015. 137(2): p. 021022.
5. Pasquali, F., et al., Method for design life of energy system components based on Levelized Cost of Energy. Journal of Cleaner Production, 2020: p. 121971.