A study of the S809 blade was conducted using a Computational Fluid Dynamics (CFD) model of the NREL Unsteady Aerodynamics Experiment Phase VI experimental rotor [8]. The results reinforced those found in the previous study that used the Blade Element Momentum (BEM) model. An increase of 3.7% is realized at cut-in speed while a 2.58% gain occurs at the rated speed. The CFD results showed similar gains to those found using the BEM model. The aerodynamic loads on the blade surface can potentially deform the cross-sectional geometry. Hence, the Fluid-Structure Interaction (FSI) analysis is used to study the effects of aerodynamic forces on the deformation of a 3D model. FSI analyzes the coupled dynamics of structures in contact with the fluid. The structural deformation occurs in response to pressure developed by the fluid. In return, the structure imparts disturbances on the adjoining fluid, and thus alters the fluid flow. The loading was also analyzed through a structural simulation of a blade segment made of ULTEM 9085. The structural analysis indicated that this material could readily withstand stresses induced by the aerodynamic and torsional loads. Moreover, the proposed design can be deformed without negative consequences on the required airfoil geometry.
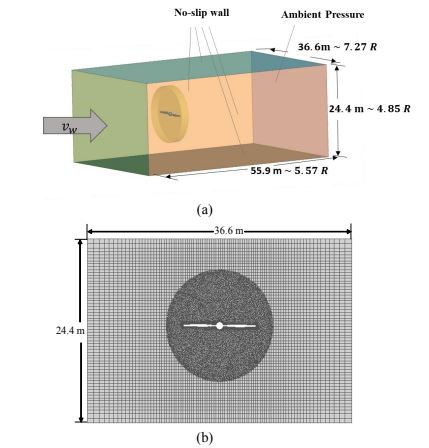
The HAWT model for (a) the computational domain and (b) overset mesh
8. Nejadkhaki, H.K., et al., A variable twist blade for horizontal axis wind turbines: Modeling and analysis. Energy Conversion and Management, 2021. 248: p. 114771.